A Comprehensive Overview to Understanding Exactly How Welding Examination Functions: Techniques, Criteria, and Finest Practices for Quality Control in Steel Fabrication
Recognizing the ins and outs of welding evaluation is essential for keeping the stability of metal manufacture. Executing best techniques can substantially boost high quality guarantee measures. The landscape of welding examination is not without its difficulties.
Importance of Welding Examination
Although welding is an essential process in various markets, its honesty directly influences the safety and efficiency of components and frameworks. Efficient welding inspection is important for identifying issues that could endanger the quality and longevity of welded joints. This process ensures adherence to developed specs and criteria, which are essential for maintaining structural stability and functional reliability.
Welding assessment offers numerous purposes, including confirming that the welding process has actually been implemented correctly, evaluating the high quality of products used, and verifying that the completed item fulfills governing and industry standards (Houston Welding Inspection). With extensive examination, possible issues such as porosity, cracks, and incomplete combination can be found early, preventing costly repair work and alleviating safety risks
Moreover, consistent welding evaluations foster confidence among stakeholders, including designers, clients, and regulative bodies, by demonstrating a commitment to quality control. The significance of welding evaluation can not be overemphasized; it is indispensable not just for conformity with lawful demands yet also for enhancing the overall efficiency of bonded structures. Eventually, a robust welding inspection program is an aggressive action that safeguards against failures, ensuring the longevity and integrity of bonded elements in their intended applications.
Common Welding Examination Methods
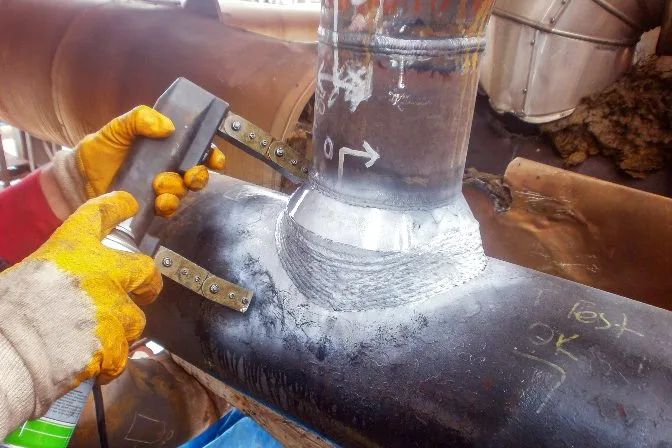
Visual examination is the first line of protection, allowing examiners to recognize surface issues such as cracks, damages, or insufficient fusion. Radiographic screening utilizes X-rays or gamma rays to expose inner defects, making it excellent for complex welds. Ultrasonic screening uses high-frequency acoustic waves to find subsurface defects, offering specific measurements of weld integrity.
Magnetic bit screening is effective for ferromagnetic materials, highlighting surface area and near-surface suspensions when bits are related to a magnetic field. On the other hand, color penetrant testing uses a fluid color to disclose surface-breaking defects, making sure that also the tiniest imperfections are spotted.
Each strategy has its staminas and constraints, commonly demanding a mix of techniques for detailed assessment - Houston Welding Inspection. By applying these evaluation methods, quality control in steel manufacture is achieved, making sure that welded frameworks meet safety and performance criteria
Sector Standards for Welding


The American Welding Culture (AWS) and the American National Specification Institute (ANSI) are two noticeable organizations that develop welding requirements. AWS D1.1, for instance, lays out the demands for welding steel structures, while AWS D1.2 concentrates on aluminum. Internationally, the ISO 3834 typical addresses high quality requirements for combination welding, providing a structure appropriate throughout national borders.

Best Practices for High Quality Assurance
Quality control in welding is extremely important to achieving risk-free and long lasting building and constructions. Applying ideal practices guarantees that every weld satisfies the called for standards and requirements. Establishing an extensive high quality management system (QMS) tailored to the specific welding task is essential. This QMS needs to specify procedures, responsibilities, and duties to mitigate risks and boost liability.
Regular training and qualification of welding workers are vital for keeping a proficient workforce. Continual education on the current welding methods and technologies makes sure that assessors and welders are experienced about present standards and methods.
Additionally, carrying out pre-weld inspections to examine materials and devices can protect against problems prior to they occur. Houston Welding Inspection. Throughout the welding process, real-time surveillance and documentation of welding criteria help identify inconsistencies instantly. Post-weld examinations should include thorough assessments making use of find out here non-destructive testing (NDT) techniques to ensure the stability of the welds
In addition, maintaining clear communication amongst employee promotes a culture of high quality. Normal audits and testimonials of the welding process assistance determine areas for renovation. By sticking to these finest practices, companies can achieve optimal high quality assurance, eventually causing boosted security and efficiency in steel manufacture projects.
Obstacles in Welding Assessment
Although welding inspection is vital for making sure architectural honesty, it offers a range of challenges that can complicate the assessment process. One significant challenge is the irregularity in welding strategies and products made use of, which can influence the uniformity of weld high quality. Different welders may employ differing approaches, bring about disparities that inspectors demand to determine and examine.
Another challenge entails the discovery of problems. Non-destructive testing (NDT) methods, such as ultrasonic and radiographic screening, can be intricate and require skilled professionals to analyze results accurately. Incorrect positives or downsides can occur, possibly leading to costly rework or compromised safety and security.
Furthermore, the existence of ecological variables, such as temperature level and humidity, can affect the stability of welds and the effectiveness of examination methods. Examiners need to likewise navigate the governing landscape, guaranteeing compliance with market requirements, which can vary by jurisdiction and application.
Conclusion
To conclude, welding evaluation plays an essential function in ensuring the integrity and safety and security of metal manufacture. Employing a selection of evaluation techniques, sticking to recognized industry requirements, and applying reliable high quality administration techniques collectively boost the reliability of bonded frameworks. Despite the difficulties faced in the evaluation process, a dedication to continual improvement and adherence to finest techniques can significantly boost the top quality assurance framework, promoting better self-confidence amongst stakeholders in the welding industry.
Efficient welding assessment is essential for determining flaws that can endanger the quality and sturdiness of bonded joints.In addition, consistent welding evaluations click here to read foster confidence among stakeholders, including engineers, customers, and regulatory bodies, by demonstrating a dedication to quality assurance.The American Welding Society (AWS) and the American National Standards Institute (ANSI) are two popular organizations that establish welding requirements. During the welding process, real-time monitoring and documentation you can try this out of welding parameters help identify inconsistencies instantly. In spite of the difficulties faced in the evaluation process, a commitment to continual renovation and adherence to ideal methods can substantially boost the high quality assurance framework, cultivating higher self-confidence amongst stakeholders in the welding market.
Comments on “Advanced Houston Welding Inspection Techniques for Accurate Results”